中国で製造された洋服・靴下・下着などアパレル用品が日本など海外へ輸出される際、製造されたアパレル用品は検品工場で検針チェック作業、製品の品質チェック、サイズ・カラーチェック、カートン入数確認を終えて、パレットに積載され国外に向けて配送されます。
検品工場内では人海戦術による品質確認も多く目視と手作業によるチェックのため作業のばらつき・作業効率・出荷製品のトレースに調査に時間がかかる点が問題となっています。
今回弊社のパッケージソフト、アパレル検品トレースシステムを導入するとカスタマイズ不要で検品作業のスピードアップと精度向上、パッキングリストの自動化が行えます。
一般的な検品運用の流れ、運用の問題点からシステムのポイントをご紹介したいと思います。
この記事の目次
・現行のアパレル検品の運用の流れ
・現行のアパレル検品の問題点
・アパレル検品トレースシステムのポイント
・アパレル検品トレースシステムの機能の紹介
・アパレル検品トレースシステム導入後の運用の流れ
現行のアパレル検品の運用の流れ
一般的なアパレル検品の流れとして、まず検針機を通す前に検針作業の対象となるカートン(箱)の品番情報とカートンの連番情報、サイズやカラーなどのSKU情報や入数を確認し、紙媒体の「作業資料」に以上の情報を記入し検針作業の準備を行います。
カートンから取り出した製品は検針機を通し、問題が無ければ箱詰めを行います。
検針機を通し箱詰めを行う際に製品のタグ情報に表示されたサイズやカラーに間違いが無いかを確認して箱詰め梱包を行います。
カートンには梱包された製品のサイズやカラーの情報、顧客名称や配送先となる仕向先の情報を手書きします。
一連の検品作業が完了すると手書きした「作業資料」を事務室に渡して「作業資料」を元に顧客別にパッキングリストをExcel作成します。
このパッキングリストには顧客名称や仕向先、ISO情報、検針した品番情報、カートン番号の一覧、各カートンに梱包された製品名やサイズ・カラーなどの情報と各数量を記載。パッキングリスト集計部分には梱包された製品枚数ならびにカートンの合計数、各品番別にサイズやカラー別のSKU小計情報を入力します。
作成したパッキングリストはパレット積みした検針後のカートンに同封して出荷を行います。
現行のアパレル検品・検針の問題点
検針作業でサイズ・カラー等の製品構成・目視による各カートンの入数チェック、箱詰めされたカートンに記載するサイズ・カラー別の数量は手書きで記入をしています。
この目視によるチェック作業と手書きの記入作業はヒューマンエラーに繋がり、誤出荷を引き起こす可能性を秘めています。同じ色の製品はサイズが違っていてもタグ情報をチェックしなければ判断ができません。毎日何千枚も検品をするため、目視による確認ではタグ情報を見落としてしまう場合もあります。
またパッキングリスト作成の元情報となる「作業資料」やカートンへ記入する「品番情報やカートン番号、サイズ・カラーの数量情報」も手書き。作業担当によって文字の書き方が違い、統一性がないので間違いを引き起こす要因の一つとなります。
パッキングリストは「作業資料」を元に作成するため、手書き資料を見ながらの入力作業は時間がかかり、入力間違いを引き起こしかねません。
またパッキングリストを確認しながら出荷作業を行うのですが、カートン選択は目視による作業のため出荷漏れや誤出荷などを引き起こす可能性があります。
アパレル検品トレースシステムのポイント
システム導入をすると、これまで目視に頼っていた製品チェック作業は全て廃止されます。全作業は製品に取り付けられている製品タグのバーコード情報をスキャンしチェック。作業チェックの精度とスピードが大幅に向上されます。
カートンに手書きで記入していたサイズ・カラーの数量情報はラベルプリンターよりカートンラベルが出力。分かりやすい文字で見やすくなり見間違いが激減。個体情報としてバーコードも印刷されます。
現場のスキャン作業が完了した後は、顧客情報を選択するだけで自動的にパッキングリストが作成。今までのような入力作業や集計作業が無くなりリアルタイムにパッキングリスト出力ができます。
また出荷作業はパッキングリスト番号と各カートンに貼られたカートンラベルのバーコード情報を元にハンディターミナルをでスキャン出荷。出荷対象のカートン個体番号を確実にスキャン確認しながら作業をするため、誤出荷や出荷漏れが防止されます。
アパレル検品トレースシステムの機能の紹介
出荷した製品にトラブルが生じた場合はカートン単位で作業履歴がシステムに保存されていますので、顧客よりカートン番号を入手すれば、「どの品番のカートン番号の検品作業をいつ行ったか」システム内で検索しスピーディな調査が可能となります。
今まで紙管理の「作業資料」やExcelのパッキングリストを元に調べていると思いますが、検品作業の日時や時刻までは確認する手段が無いため、アパレル検品トレースシステムの導入で精度の高い調査結果を顧客へ提供することが可能となります。
アパレル検品トレースシステムの機能のご紹介
タッチパネル採用で省スペース化
弊社のアパレル検品トレースシステムは、現場利用はタッチパネル式を採用。現場にキーボードやマウスなど周辺機器の準備は不要、省スペース対応です。
タグスキャンで正確スピーディ
製品タグのバーコードをスキャン。製品情報を読み取ることで目視作業よりも効率的にスピーディに作業を行えます。
見やすいカートンラベル採用
ラベルプリンター発行のカートンラベルを採用。作業ミスに繋がる見難い手書き管理を廃止。
リアルタムに出力できるパッキングリスト
スキャン検品結果はリアルタムに事務所と連動。検品作業完了後すぐにパッキングリストが作成され、日本側からの早急な依頼にもスピーディな対応が実現されます。
パッキングリストの必要項目は全て自動集計
パッキングリストで面倒だった「作業資料」の入力作業やSKU単位の集計作業は一切なく、顧客情報を選択するだけで自動的にパッキングリストが作成され手間が大幅に削減されます。
デジタル管理でカンタン検索
顧客情報や品番情報、作業履歴はデジタルデータで管理。カンタンに検索と調査が行え、今までのような台帳をめくりながらの調査は無くなります。
顧客情報と工場・仕向先の紐付け管理を採用
顧客情報として工場名と仕向先を紐付けてして管理。カートン単位で仕向先管理を行うのでパッキングリストにカートン単位の仕向先が印刷され仕向先の確認が楽になります。
ハンディターミナルでデジタル出荷作業
出荷作業はカートンラベルのバーコードとパッキングリストを活用してハンディターミナルでチェックをしながら行えます。ハンディターミナルに出荷情報が表記されるので今までのような目視確認による出荷作業の誤出荷、出荷漏れを防ぐことができます。
アパレル検品トレースシステム導入後の運用の流れ
システム導入後の作業の流れは今までと基本的に同じですが、人間の目や手による作業が一切無くなります。
検針機を通った製品はスキャナーでタグのバーコードをスキャン。自動的にサイズ・カラーの数量チェックを行います。また単一品出荷時にサイズやカラーが異なる製品が混載した場合も自動的にエラー表示されるので誤出荷を防止することができます。
カートンラベル発行で個体認識。ラベルにはスキャン結果が印刷されますので、手書き記入は不要です。
全ての検品作業が終わった後は事務所でパッキングリストを出力。顧客名を選択するだけで、必要なパッキングリストが自動的に出力されます。
出荷時はパッキングリストを元にハンディターミナルの指示に従い、対象カートンをスキャン出荷。作業ミスがあるとエラー警告、作業完了時はアナウンス表示されます。
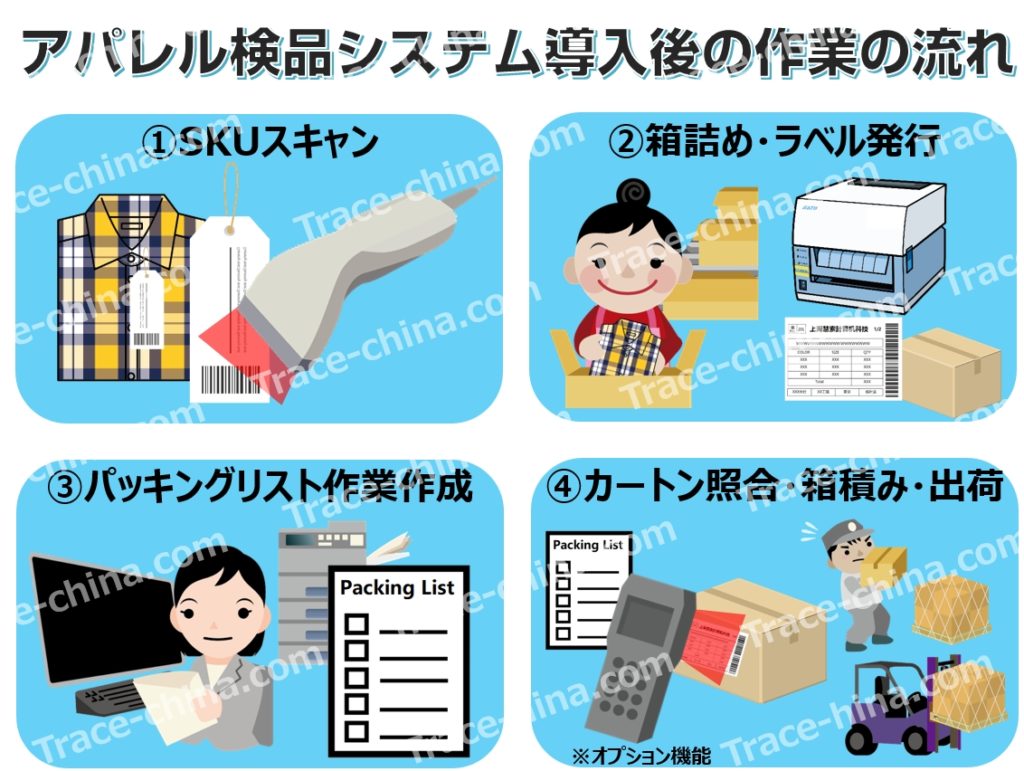
人海戦術でミスが絶えず作業効率がなかなか上がらなかった検品作業にお悩みの企業様。またはコストパフォマンスの高い検品作業にご興味がある企業様、是非お問い合わせ下さい。